Case study
Repairing a gear drive for a major steel mill
Timken Power Systems (TPS) coordinated an end-to-end solution. It began with the overhaul of a gearbox that operated a basic oxygen furnace (BOF) in the heart of a large steel producer’s plant. It became a multi-phase upgrade and on-site install of an entire drivetrain responsible for the critical operation of a much larger 110-ton converter.
According to Mike D’Angelo, Timken Power Systems National Sales Manager for the US., “the plant’s original 75-ton converter needed to be upgraded to handle 110-ton capacity. Once we performed a gear train analysis, it was evident that the converter’s higher production loading would result in accelerated wear for the current gearbox design.”
Along with the necessary gearbox improvement, the TPS team was also challenged to upgrade the drivetrain’s DC system to an AC VFD system.
“We shifted our focus to a far more comprehensive solution,” says D’Angelo. “We were now responsible for overhaul of the main BOF gearbox that tilts the converter vessel, four primary units that drive it, as well as new AC motors and a VFD control system.” Added to this configuration was a new, TPS-designed air motor backup system with brakes. This added level of protection helps avoid potential risk of the massive converter vessel being improperly tilted during a power outage.
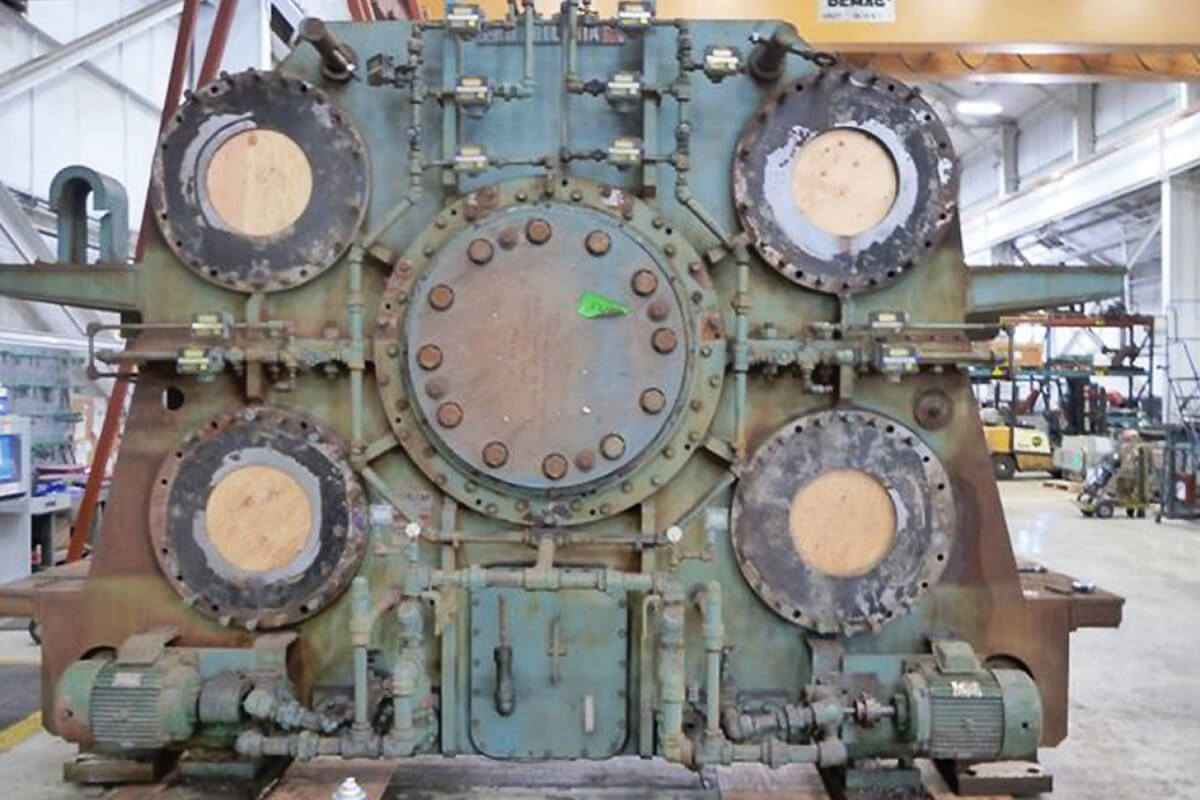
The integrated solution required to support this shift from overhaul to upgrade came naturally to the TPS team, through the coordinated contribution of:
- Philadelphia Gear: Overhaul of main BOF and four primary gear drives to accommodate (4) AC motors on inboard side; relocation of (2) air motors/Hamilton H1070 and brakes to outboard side; and torsion bar assembly
- Smith Services: VFD/PLC system and AC motors
- Standard Machine: (2) Hamilton H1070 units, mounting pads, and torsion bar machining
- Onsite Technical Service team: On-site install/ commissioning; and post-specification improvements
3-D modeling every step of the way
Before the project began, a sophisticated 3-dimensional model was created. Showing all aspects of the installation, from every conceivable angle, it became an essential tool for both TPS and the customer through each phase of planning and implementation.
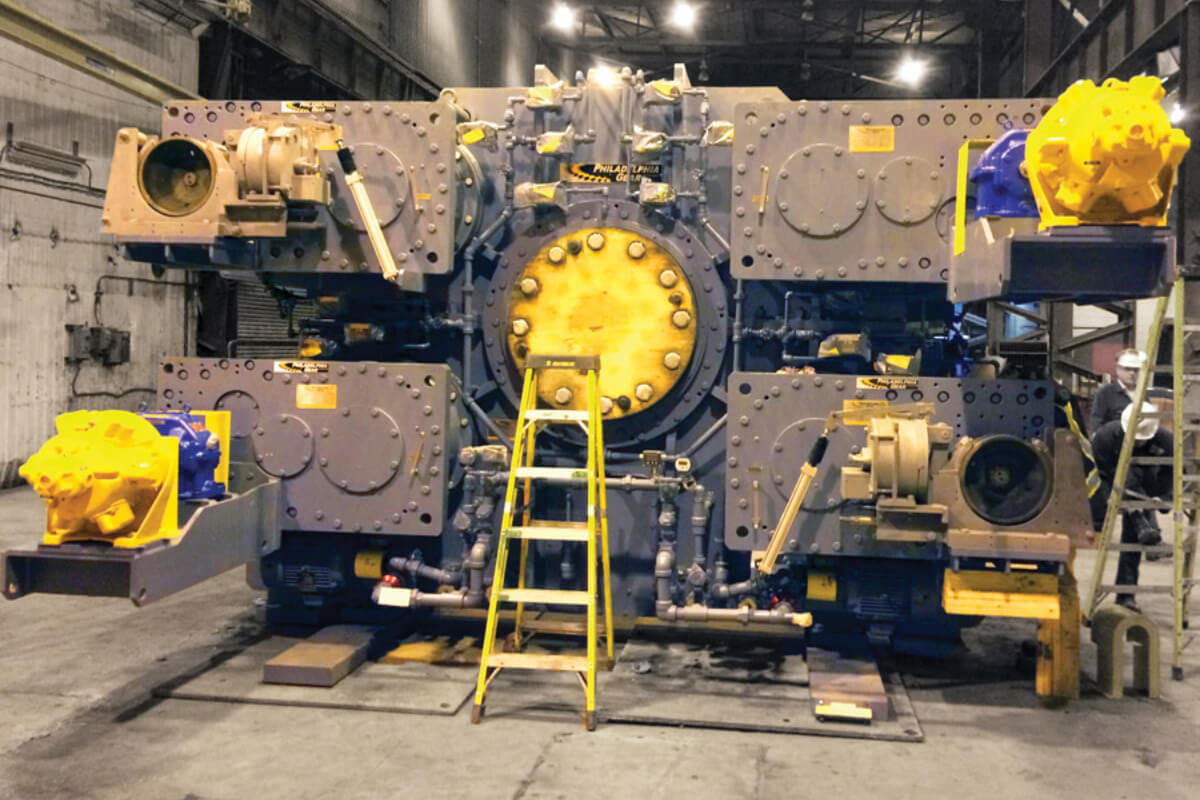
“The TPS team is built for demanding applications that require sophisticated levels of electromechanical design, implementation and support.”
Results that matter
Beyond the electromechanical upgrades to this mission critical application, the long-term effects of the TPS solution means reduced energy consumption, softer startup capabilities, efficient load sharing, and extended equipment life. These positive results have led to the overhaul of a second main BOF and two additional primary gear drives.