Case study
Arctic mine saves maintenance costs, improves service life with Standard Machine
THE PRIMARY CHALLENGE
Working within the rugged and unforgiving Arctic circle, one Canadian oil sand mining company operates eight massive electric rope shovels across several sites to harvest crude oil and bitumen. The raw materials are used to make fuel and other products for the road surfacing and construction industries.
Application requirements in this environment are extremely tough on transmissions and other mechanical systems. Temperatures range from -50°C (-58°F) in the winter to 45°C (113°F) in the summer. Each shovel’s dipper payload is 90 tons, with a working weight of more than two million pounds.
Under these conditions, each shovel’s propel planetary transmission experienced significant wear and tear. Instead of opting for repair, site maintenance teams routinely scrapped and replaced the transmissions with new units. Replacement was far more economical than repairing the transmissions due to the high cost and short service life of the twin ring gears in the original equipment manufacturer’s (OEM’s) transmission design. To repair a damaged ring gear, which measures about six feet in diameter, during a scheduled transmission rebuild costs about 75% the price of replacing the entire transmission.
During an onsite visit to one of the mining sites, experts from Standard Machine, a part of Timken Power Systems, identified the root cause of the problem. The OEM’s twin ring gears were made from an inferior material, which was prone to pitting and wore out quickly.
We previously observed this same problem at a separate coal mining operation in British Columbia,” said Jamie Wilson, Subject Matter Expert — Mining. “In that case, we had success reverse engineering the ring gear and manufacturing it to a much higher material standard.”
THE SOLUTION
The mining site’s maintenance team chose to have Standard Machine rebuild the propel planetary transmission, replacing the old ring gear with a new forged component.
Standard Machine completed the rebuild at its manufacturing and service center in Saskatoon, Saskatchewan.
“We have deep knowledge of how to manufacture various types of drop-in replacement planetary gearboxes for a wide range of applications,” Wilson noted. “We leveraged that experience as well as our strategic supply chain to procure a high-quality ring forging. Our manufacturing team expertly machined the ring and cut the internal gear teeth. This ensured proper fit and performance once it was incorporated back into the rebuilt transmission.”

KEY RESULTS
Standard Machine rebuilt the first transmission, incorporating the new ring gear, in 2013. When the same transmission was due for rebuild again in 2021, the team discovered that the forged ring gear was in great condition. Minor repairs were applied and the ring gear was reused in the transmission rebuild for another seven years of service. It is estimated that forged ring gears can be repurposed in two consecutive rebuilds before needing replaced. In addition, the Standard Machine solution extends the customer’s overall transmission life from five to seven years before a rebuild is required.
While just one mining site paid nearly a half million dollars every five years for a new transmission, Standard Machine’s rebuilds have saved them roughly 50% off the cost of buying new. The overall maintenance process for the shovel is also more efficient. On average, a rebuild can be completed in about half the time it takes to procure a new transmission from the OEM.
Today, Standard Machine works with the mining company to rebuild all eight of its shovels’ transmissions on a routine maintenance schedule. It also conducts repairs on the shovels’ hoist, crowd and swing transmissions, and supports transmission repairs for the operator’s fleet of electric shovels.
“This equipment is working in some of the harshest conditions in the world,” Wilson said. “It’s our job to ensure the customer get the most value they can from their machinery, in terms of performance, productivity and budget.”
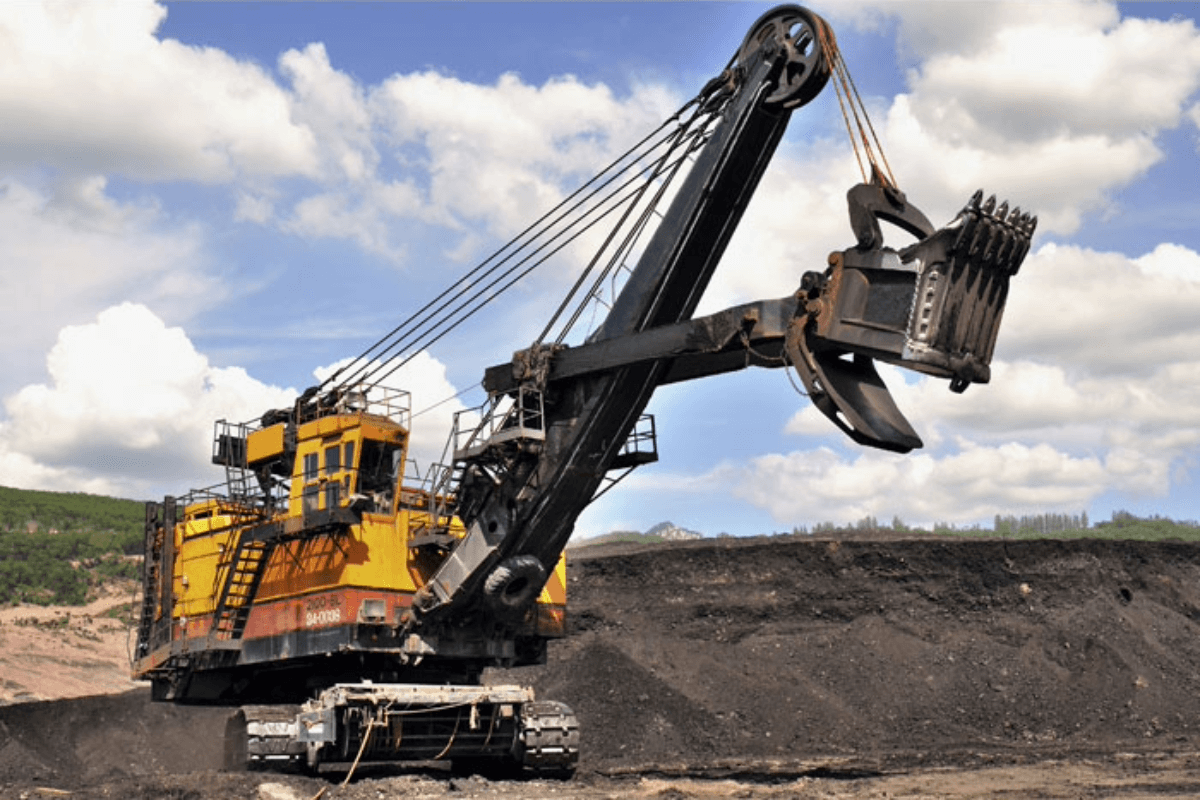