We provide gear service & gear repair every gearbox brand
- Allen Gear
- Amarillo
- BHS-Voith
- Black Clawson
- Brad Foote
- David Brown
- John Brown
- Chemineer
- Cleveland
- Delaval Steam Turbine*
- O. James
- Elliott
- Falk
- Farrell
- Flender
- Flender-Graffenstaden
- Foote Jones
- General Electric
- Hamilton Gear*
- Hansen
- Hitachi
- Horsburgh & Scott
- Lightnin
- Link-Belt
- Lufkin
- Maag
- Marley
- Mitsubishi
- Nuttal
- Philadelphia Gear*
- Philadelphia Mixers
- Renk
- Siemens
- Standard Machine*
- Sumitomo
- Thyssen
- WesTech*
- Western Gear*
- Westinghouse*
*Philadelphia Gear, WesTech, Western Gear, Delaval Steam Turbine, Standard Machine, and Hamilton Gear are all registered trademarks of The Timken Company or its affiliates.
Keep operations running with emergency overhaul servicesDon’t let an equipment failure derail your business. Our gear service team is available 24/7 to help prevent downtime and keep you on schedule.
How it works
-
1
Reach Out
-
2
Initial inspection
-
3
Disassembly, cleaning, and gear repair
-
4
Assembly and testing
-
5
Painting, preserving, and shipment
-
6
Rest easy
1 Reach Out
Our team is standing by and ready 24/7 to help with your toughest gearbox challenges. Contact our experts today and send photos of your equipment or speak to a Standard Machine sales professional to come to your location to evaluate your equipment. In many cases, gearbox replacement costs can be 3-4 times more expensive than gearbox repair. We can assess the condition of your gearbox and provide a cost-effective solutions tailored to your needs.
2 Initial inspection
Whether onsite or at our facility, our specialists will inspect your gearbox to identify the root cause of the failure. After the inspection, we will provide you with a detailed report that includes gear repair recommendations, images of the damage, the gear repair cost (or gearbox replacement cost if recommended), and a timeline for the project.
3 Disassembly, cleaning, and gear repair
Once the gear repair scope is approved, our experts will take apart and clean the unit, using gearbox reverse engineering to analyze its components before scheduling the replacement industrial gearbox parts to be manufactured. For upgrading your equipment to handle higher horsepower or more torque, our engineers will evaluate the changes and make necessary changes and incorporate them into the manufacturing process, if they find them feasible.
4 Assembly and testing
After the components have been created, we will reassemble and rigorously test the gearbox — measuring endplay, tooth contact and backlash, temperature, sound, vibration levels, and more. This step is crucial, since it identifies any lingering issues and ensures, reliable, safe, and efficient performance in real-life conditions.
5 Painting, preserving, and shipment
Next, we will apply epoxy paint and preserve the unit for storage. After the unit is dried and preserved, we will send your gearbox to you along with all documentation.
6 Rest easy
Have peace of mind with our best-in-industry three-year warranty for all repairs performed at our gear service and manufacturing facility. If any issues do arise, simply contact our expert gearbox repair team to quickly get back up and running.
Nestled in central Saskatoon, our shop delivers accessible gear replacement, maintenance, and gear repair near you, complemented by reverse engineering support at our facility or at your location, so you can rest assured knowing your needs are met precisely where you are.
Don’t let an equipment failure derail your business. Our gear service team is available 24/7 to help prevent downtime and keep you on schedule.
How it works
-
1Reach Out
-
2Initial inspection
-
3Disassembly, cleaning, and gear repair
-
4Assembly and testing
-
5Painting, preserving, and shipment
-
6Rest easy
1 Reach Out
Our team is standing by and ready 24/7 to help with your toughest gearbox challenges. Contact our experts today and send photos of your equipment or speak to a Standard Machine sales professional to come to your location to evaluate your equipment. In many cases, gearbox replacement costs can be 3-4 times more expensive than gearbox repair. We can assess the condition of your gearbox and provide a cost-effective solutions tailored to your needs.
2 Initial inspection
Whether onsite or at our facility, our specialists will inspect your gearbox to identify the root cause of the failure. After the inspection, we will provide you with a detailed report that includes gear repair recommendations, images of the damage, the gear repair cost (or gearbox replacement cost if recommended), and a timeline for the project.
3 Disassembly, cleaning, and gear repair
Once the gear repair scope is approved, our experts will take apart and clean the unit, using gearbox reverse engineering to analyze its components before scheduling the replacement industrial gearbox parts to be manufactured. For upgrading your equipment to handle higher horsepower or more torque, our engineers will evaluate the changes and make necessary changes and incorporate them into the manufacturing process, if they find them feasible.
4 Assembly and testing
After the components have been created, we will reassemble and rigorously test the gearbox — measuring endplay, tooth contact and backlash, temperature, sound, vibration levels, and more. This step is crucial, since it identifies any lingering issues and ensures, reliable, safe, and efficient performance in real-life conditions.
5 Painting, preserving, and shipment
Next, we will apply epoxy paint and preserve the unit for storage. After the unit is dried and preserved, we will send your gearbox to you along with all documentation.
6 Rest easy
Have peace of mind with our best-in-industry three-year warranty for all repairs performed at our gear service and manufacturing facility. If any issues do arise, simply contact our expert gearbox repair team to quickly get back up and running.
Nestled in central Saskatoon, our shop delivers accessible gear replacement, maintenance, and gear repair near you, complemented by reverse engineering support at our facility or at your location, so you can rest assured knowing your needs are met precisely where you are.
Extend your equipment’s life with gearbox upgrades
Explore our comprehensive selection of upgrade gear services.
Gearing upgrades
|
Lubrication upgrades
|
Bearing upgrades
|
Smart add-ons
|
The detail to get the job done right
Instead of taking a cookie-cutter approach, we can reverse engineer every gearbox or component to meet exact OEM standards and the specific needs of your industrial application.
With training in gearbox failure root cause analysis, our experts carefully deliver full disassembly and cleaning, inspection and measurement, engineering evaluation and recommendations, and gearbox repair and spin testing.
That’s how Standard Machine has become Canada’s leading name for reliability — for every brand.
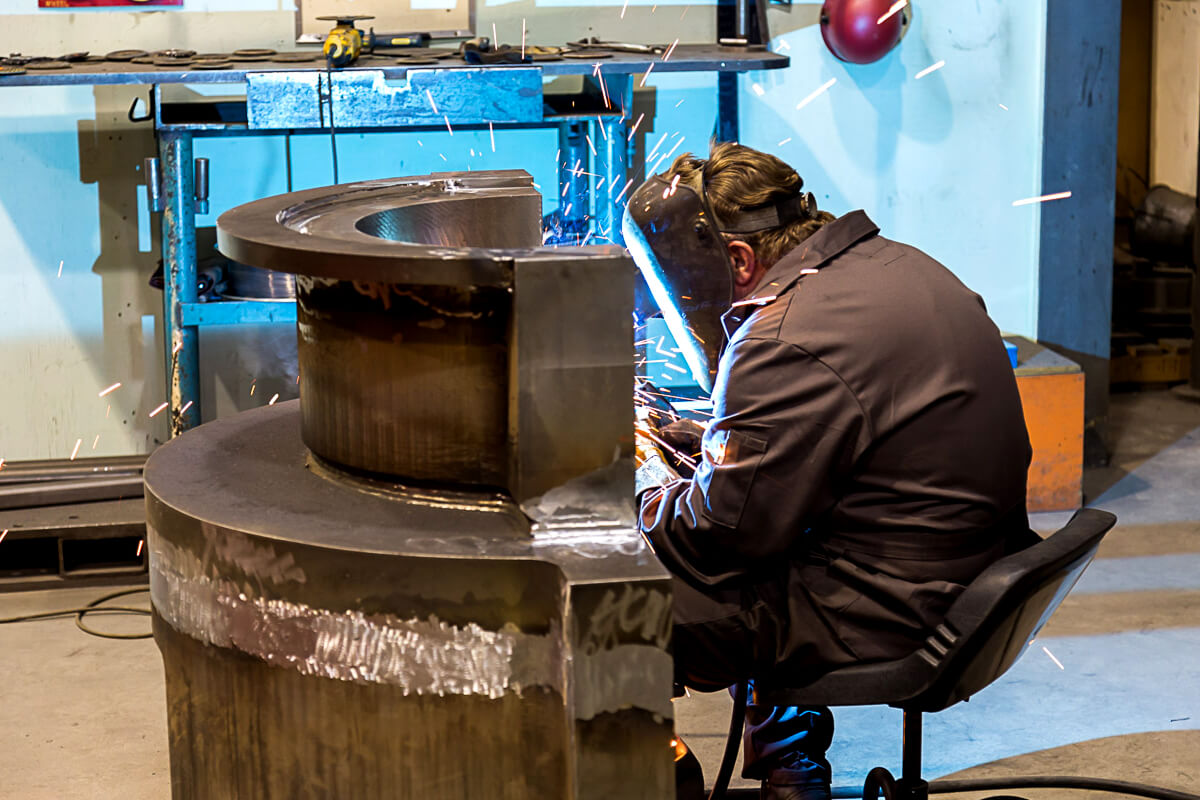
Don’t let repairs stall your operations. Contact Standard Machine today.Our experts are standing by to help keep your application running. Contact us today for a quote to find out more about our gearbox repair, service or gearbox replacement costs. Start the conversation today.
CONTACT USREQUEST A PART
Our experts are standing by to help keep your application running. Contact us today for a quote to find out more about our gearbox repair, service or gearbox replacement costs. Start the conversation today.
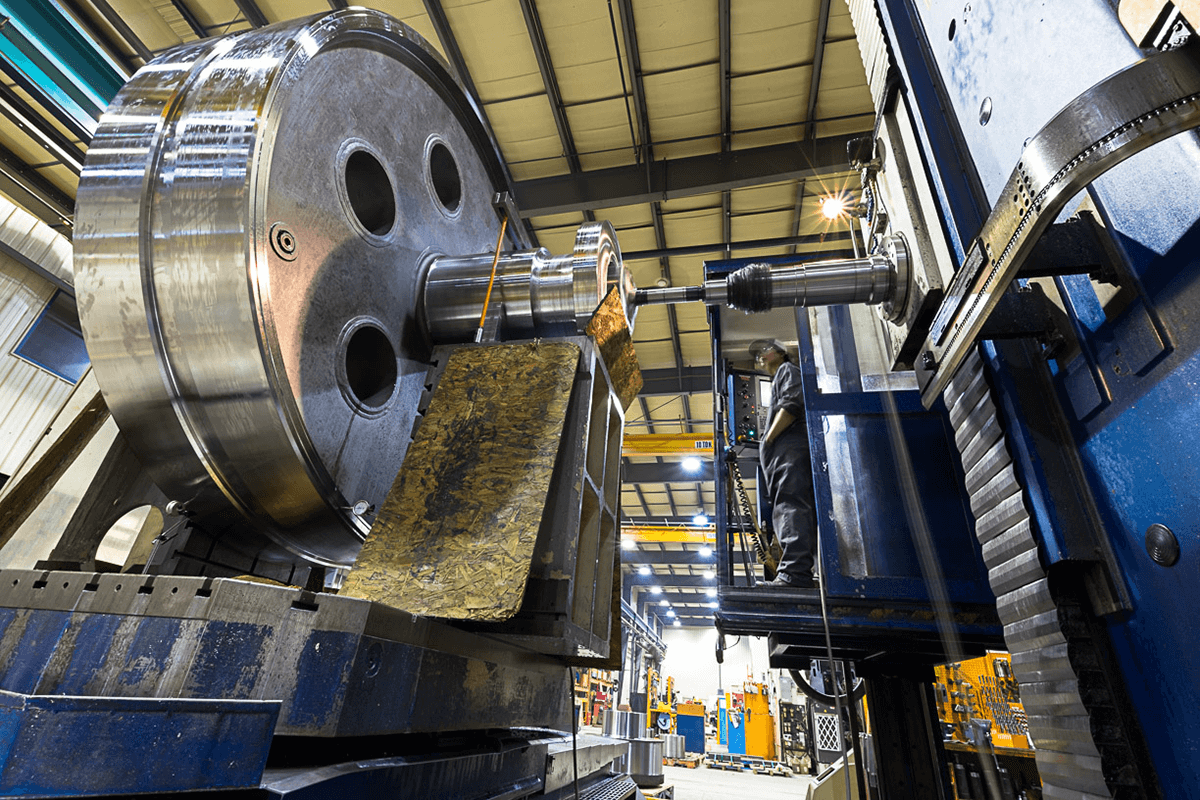