Standard Machine provides precision pinion gearing, rolling mill drives, and gear reducers engineered to meet the heavy-duty, varied needs of the steel and metal processing industry. Beyond manufacturing, we deliver inspection and upgrade services and can determine the proper metallurgical properties and AGMA quality for your custom application. Plus, we can increase load-carrying capacity within the existing unit size by utilizing upgraded gear element designs and processes that improve tooth contact to provide more accurate gearing.
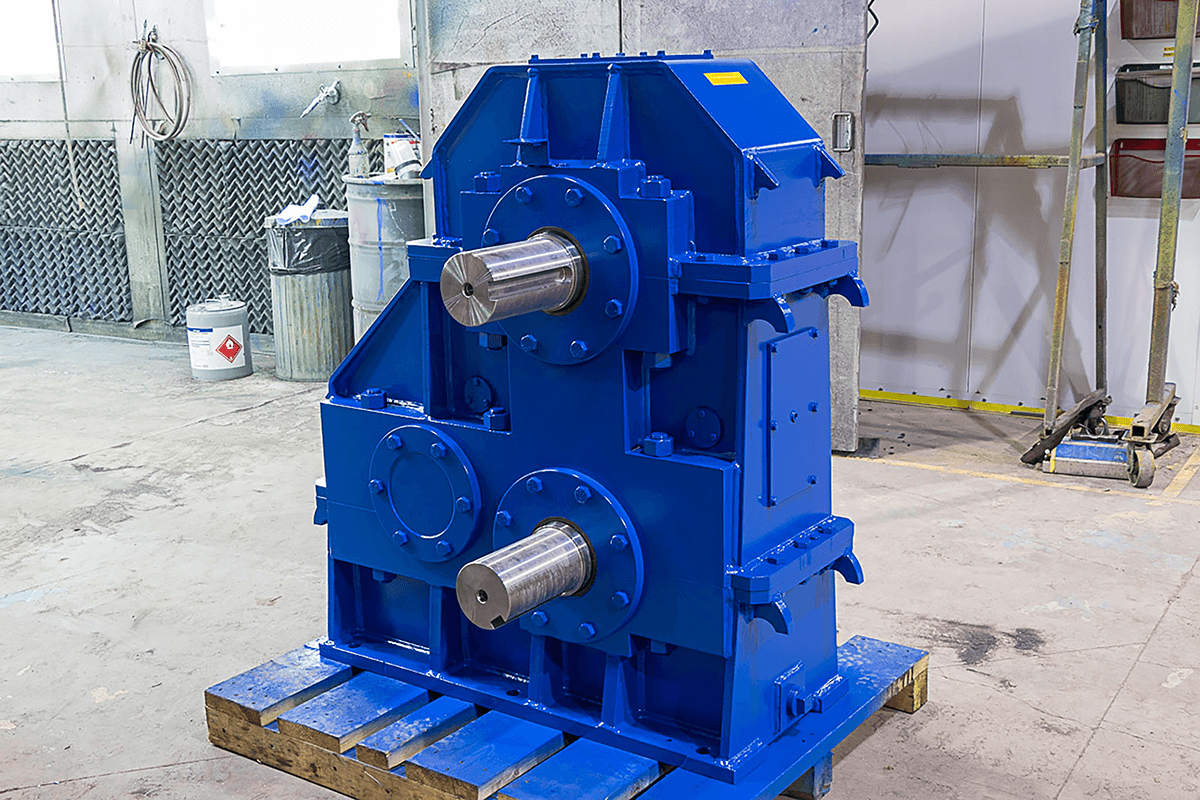
One-stop metal processing drivetrain solutions
As a part of Timken Power Systems (TPS), Standard Machine works with our gearbox, electric motor, and bearing repair facilities to provide complete electromechanical design and repair expertise for your entire drivetrain.
Custom gearbox manufacturing and repair
Whether it’s designing and manufacturing a new gearbox or replacing an existing one, our gearbox configurations meet a wide array of size and footprint variations. We can create any possible gear arrangement to your requirements: from parallel shaft to right-angle, to double helical, to planetary/epicyclic, to bevel helical, and more. There is virtually no gear-related challenge that we haven’t seen – and solved – before.
Each of our ISO-certified regional service and manufacturing centers is equipped to provide equipment decision-makers with the data they need to make informed decisions. Our service centers can reverse engineer any gear drive or component to exact OEM specifications, servicing virtually any brand. And by performing a detailed design review of both the gearbox and its application, our technicians can determine the uprate potential of the unit.
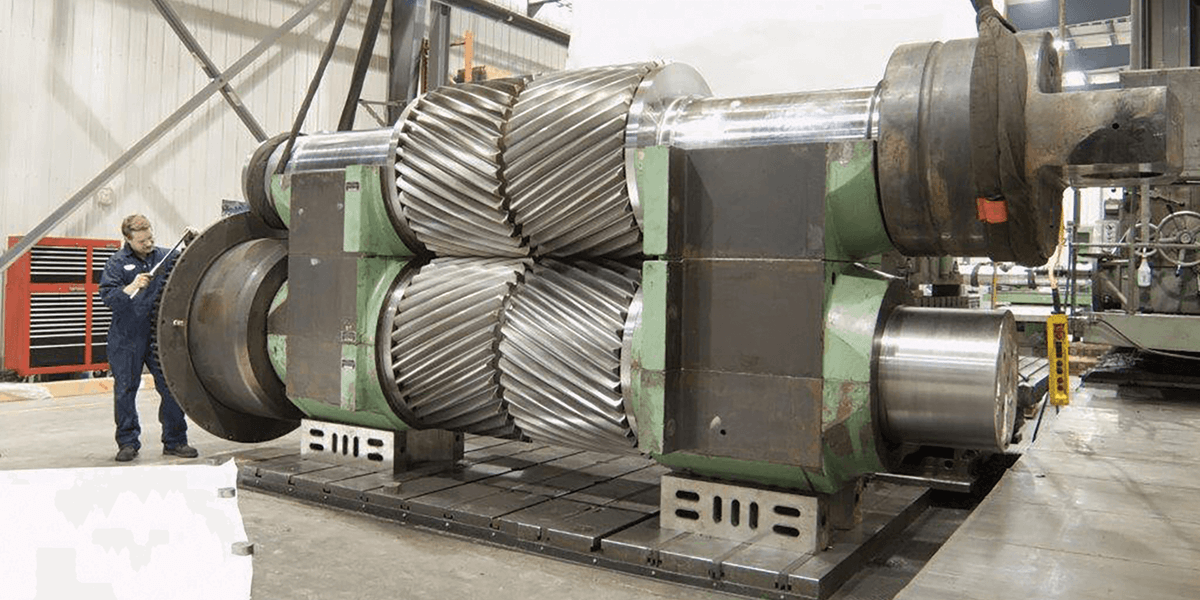
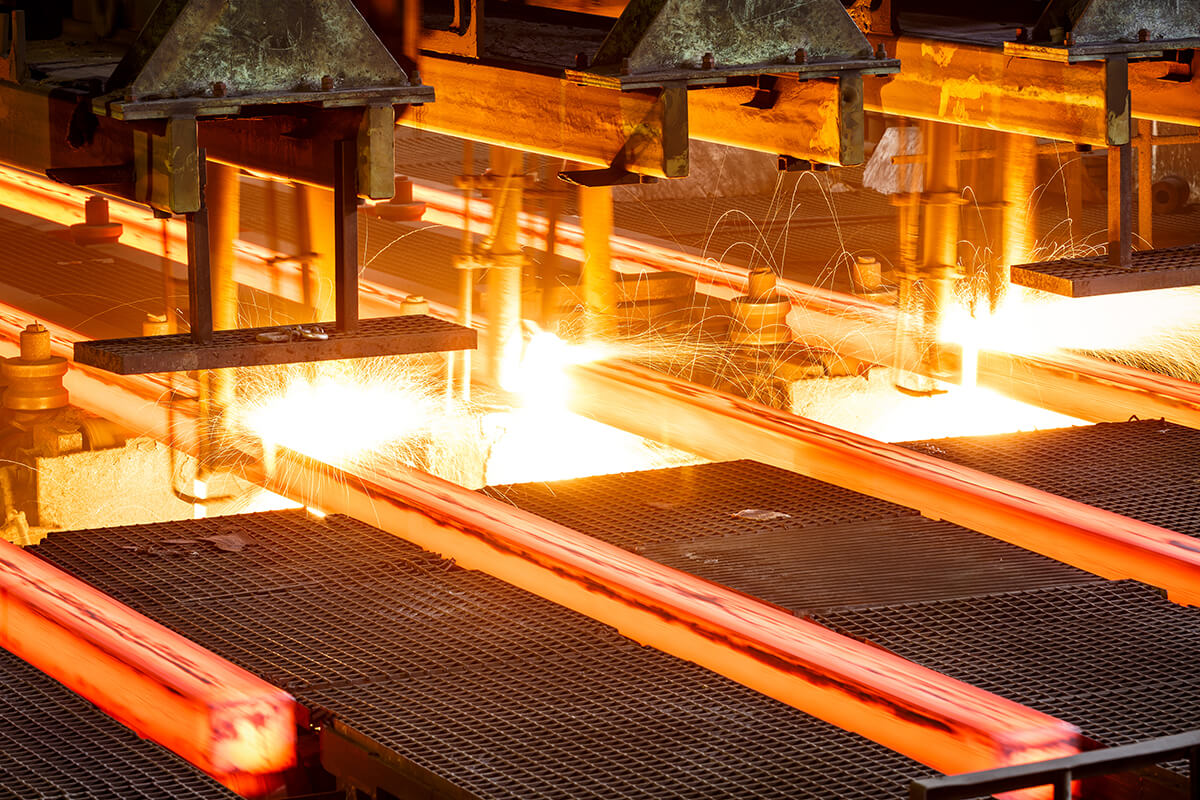
We can provide new or replacement gearboxes for any of the following processes and applications:
- Bar mills and edgers
- Basic oxygen furnaces
- Coilers/uncoilers
- Cold reduction mills
- Continuous annealing
- Galvanizing
- Hot strip mills (main drives inion stands)
- Pickle lines
- Steckel mills
- Tension reels
Inspect, repair, and upgrade services
Standard Machine delivers quick turnaround times for the inspection and overhaul of mission-critical gearboxes. Each of our facilities is staffed with world-class engineers and shop technicians outfitted with state-of-the-art machinery to ensure we hold to exact OEM specifications. We perform unmatched gearbox failure root cause analysis and can provide full disassembly and cleaning, inspection and measurement, and engineering evaluation to determine scope of work recommendations for every gearbox we receive — all backed by a leading three-year repair warranty.
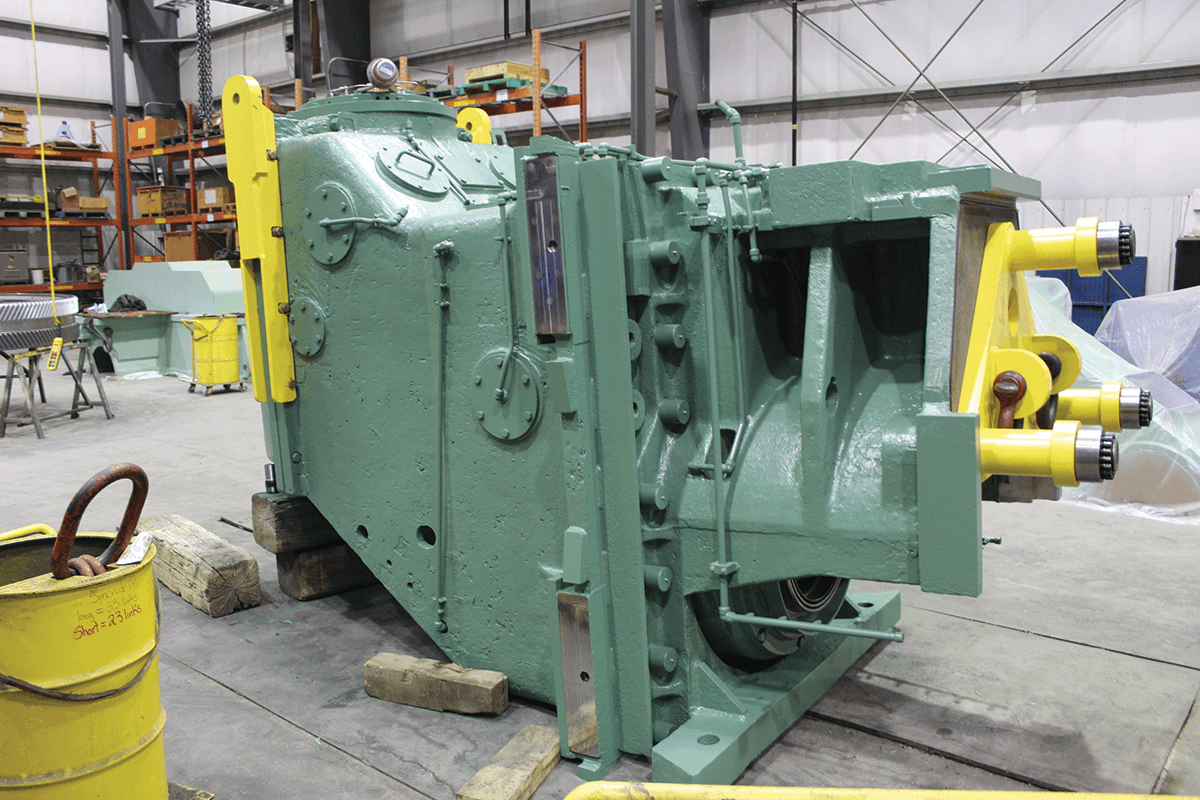
Onsite Technical Services (OTS)
Resolve your gearbox and drivetrain issues while the equipment remains in-place. We can provide all these services at your work site:
- Failure analysis with full documentation
- Removal and reinstallation of gearboxes, motors, and generators
- Alignment services including laser, optical, and reverse
- Balancing of rotating elements
- Engineering and reverse engineering of components
- Grouting of foundations and equipment
- Housing re-boring and in-place machining
- Journal and gear hardness checks
- Keyway cutting, line boring, and welding
- Non-destructive testing including magnetic particle inspection
- Millwright services
- Oil sampling and analysis
- Preventative and predictive maintenance programs
- Temperature readings by infrared laser
- Ultrasonic testing and vibration analysis
- Yellow gear marking compound for tooth contact checks
- Design and installation of control systems (including VFDs)
Open gearing and OEM parts
Standard Machine utilizes the latest in gear production in the manufacture of precision gearing for metal processing applications. We employ proven tools and decades of experience to get the job done right, every time.
- Precision gear form grinding: Custom-built gear grinders capable of precision tooth grinding from the smallest pinions to large bull gears up to 4 meters in diameter
- Gear hobbing, shaving, and lapping: Utilize ultra-precision gear cutters for cutting even the largest of gears
- Turning and boring: Wide range of technology to fit the needs of each job, from horizontal boring mills for excessively large and heavy gear cases to CNC machine centers for the production of multiple work pieces
- OEM renewal parts and custom services
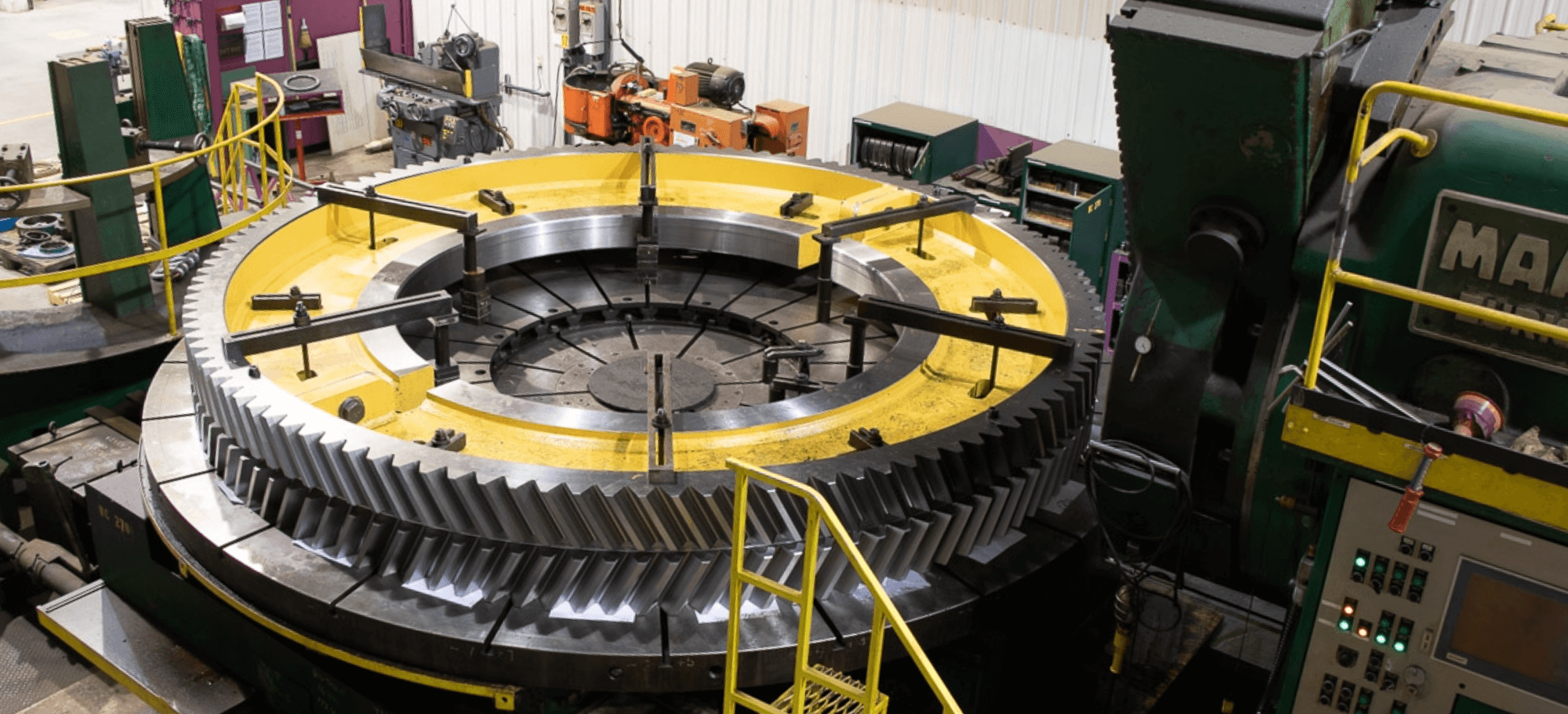
Learn how Standard Machine can solve your metal processing gearbox challengesConnect with our experts to get precision-engineered support built specifically for your demanding applications.
CONTACT US
Connect with our experts to get precision-engineered support built specifically for your demanding applications.
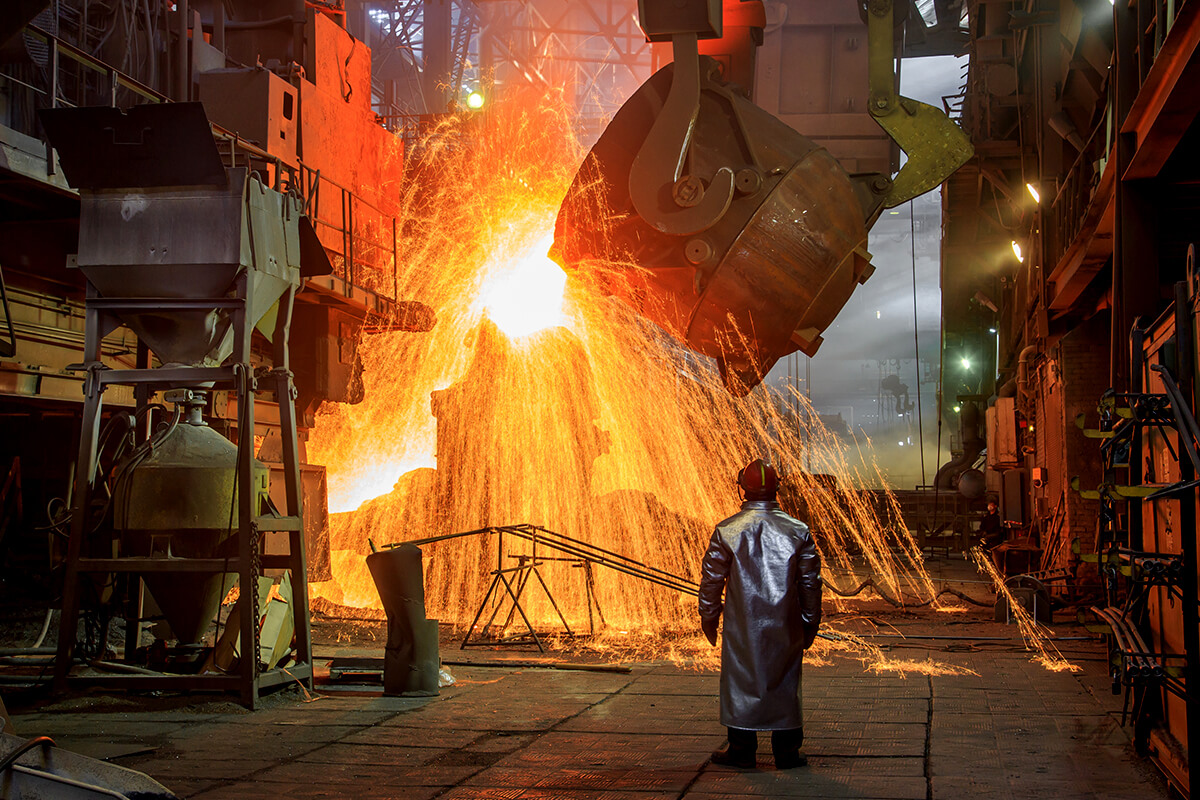